The failure of a cargo pump onboard a newbuild tanker has highlighted the need for crews to regularly monitor rotating machinery for excessive wear and vibration, if unnecessary downtime and costs are to be prevented.
The German owner took delivery of a 2021-built chemical tanker from a Chinese yard in 2021, but the long shaft driving the cargo pump’s impeller was not correctly installed, destroying the pump beyond repair and delaying cargo loading operations.
CM Technologies’ Sales Director Uwe Krüger cites other examples where ships’ pumps appeared to be in sound condition, but were in fact close to being written off.
“During the physical inspections of three pumps aboard a 58,000dwt containership, initial checks indicated acceptable values for balance and shaft alignment, but a second test using our Vibration Meter Marine immediately alerted the crew to a bearing close to seizure,” he said.
The bearings on all three cargo pumps were found to have the same potentially catastrophic pitting damage, requiring costly overhaul.
“Ships’ fire, freshwater, cargo, sewage and ballast water pumps are critical but often overlooked pieces of machinery,” said Krüger. “Yet, despite the importance of the humble pump to ship operations, rotating machinery is still often only monitored and serviced on fixed maintenance schedules. Pump failure can place the can place ship, cargo and crew at risk.”
CMT recommends that regular vibration analysis should start at system commissioning and continue throughout the operational life of the vessel. An on-going monitoring strategy is crucial to maintaining the service life of rotating equipment, troubleshooting problems, and preventing failures, and subsequent costs,” he said.
CMT’s Managing Director Matthias Winkler furthered: “A replacement bearing can cost as little as US$20. But finding out you needed one after the motor has burnt out could easily cost thousands of dollars to put right. And Murphy’s Law dictates that this is likely to happen in a Port Said or somewhere while the next available motor can be found in Rotterdam or Singapore, so you can add significant logistics and agent costs on top of that.”
Columbia Shipmanagement and Hamburg based shipping group RHL Reederei Hamburger Lloyd are just two shipping companies that have been using CMT´s Vibration Meter Marine since the product was unveiled in 2015.
“These ship managers wanted a monitoring system capable of immediate analysis of existing problems without requiring the user to have any special knowledge, explained Winkler. “Regular use of the system has alerted crews to bearing defects before breakdown, averting costly damages. The technology has already justified the investment.”
Vibration analysis provides insights into the most common cause of machinery damage and reduced service life. Bearing damage is particularly prevalent, caused by shaft misalignment, insufficient or incorrect lubrication and general wear and tear. Pump health can be easily assessed by analysing vibration.
“Crews of seagoing vessels are under constant stress, and crew changes occur at fixed intervals, so vibration monitoring devices need to be easy to use with measurement readings that are simple to understand by crew members with limited technical knowledge.
“Our Vibration Meter Marine is a powerful, expert system that provides on-the-spot usable results without the need to send information to shore for evaluation. Even beginners can understand what the readings are telling them,” said Winkler.
Alongside a range of vibration meters, monitors, software and analytical tools, the CMT´s Vibration Meter Marine has been specifically designed for the harsh marine environment. The hand-held device, acceleration sensor, software, and accessories are delivered in a small, rugged case designed for easy storage in between usage.
The meter also includes a mode to monitor the lubricating performance of greased, water, or oil lubricated bearings in pumps and rotating machinery. As an option, data can be stored for trend analysis using the diagnostic software.
“Our goal is to provide crews and superintendents with a practical solution that will enable them to detect pump problems early and shift from fixed inspection schedules to more effective condition-based protocols. Vibration analysis does need to be part of the regular machinery checks crews make on their rounds.”
[ENDS]
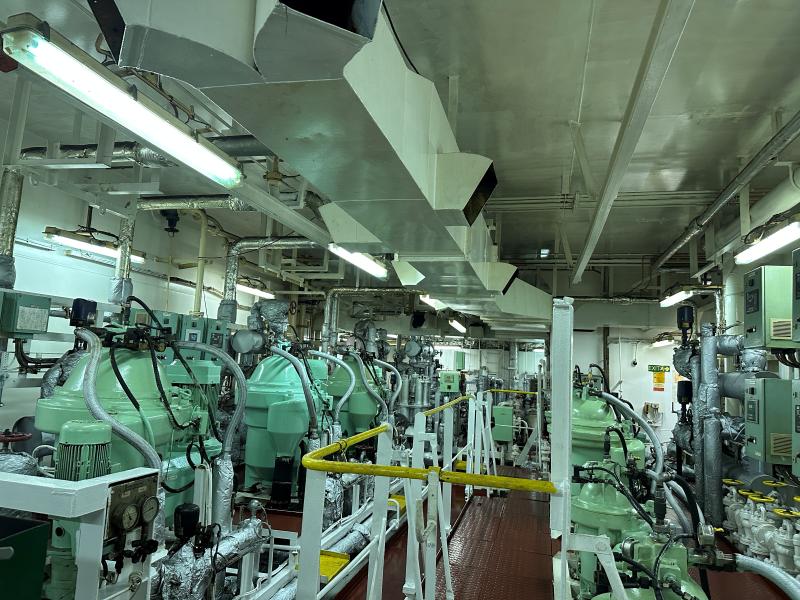
About CMT
Founded in 2003, CM Technologies GmbH and is one of the world’s leading providers of testing and monitoring technology. CMT is the recognised expert in machine health monitoring, fuel and lubricant analysis and water testing. The company’s world renowned PREMET range of Diesel Performance Monitoring technology can be traced back to engine pioneer James Watt.
When engine failure isn’t an option, visit https://cmtechnologies.de/en