Marsh Brothers Aviation (MBA), a leading manufacturer of advanced polymer seal and bearing solutions for the aviation industry, has received Transport Canada approval for its innovative new King Air Flap Roller Bearing.
The revolutionary new product – the first polymer bearing solution Marsh Brothers Aviation has developed for commercial aircraft – solves a critical maintenance issue faced by operators of the popular Beechcraft King Air series of aircraft.
“We can now provide a long-life roller/bearing solution that improves safety, reduces operating costs, and increases aircraft availability for the country’s King Air operators,” says Nicholas Choo-Son, Director Business Development at Marsh Brothers Aviation.
OEM greased needle flap rollers are prone to seizing up over time as the grease ages and stiffens. This then causes the flap rollers to slide in the track instead of rolling, leading to abnormal track wear and damage resulting in unscheduled downtime, and costly repairs.
“The style of roller currently used is a traditional sealed grease packed needle roller that relies on supplemental lubrication,” says Choo-Son. “Grease does not respond effectively to the lower outside air temperatures at flight altitudes, so the rollers can slide in the track rather than roll.”
Choo-Son says this is a well-known problem amongst the King Air community, with mandatory 3000-hour inspections frequently revealing bearing wear and aluminum track damage.
“Unscheduled maintenance from a seized flap roller can easily cost operators in excess of US$20,000 in parts and labour, plus substantial revenue losses from aircraft downtime,” he says.
MBA believes that once operators convert to the self-lubricating polymer bearing alternative, inspections will reveal little to no bearing wear and zero metal-on-metal deterioration of the aluminum track.
“This is a breakthrough development for King Air operators in Canada and, following any subsequent approvals from FAA and other authorities, across the U.S.A and beyond,” says Marsh Brothers Aviation’s Business Development Manager, Juan Rivera.
“The King Air flap roller demonstrates our expanding capabilities and commitment to delivering advanced polymer solutions that make aircraft safer and more cost effective to operate.”
MBA’s proprietary AeroTough® material, the self-lubricating polymer on which the new roller bearing is cited as having greater durability than other materials, including Teflon®.
What’s more, compared to the original greased metal bearings used in these and other aircraft, the rollers last considerably longer. The single-piece design of the King Air Flap Roller Bearing also simplifies installation, compared to the OEM system.
“A new roller design that does not rely on supplemental lubrication addresses the need for a better and more reliable roller,” says Rivera. “And by means of having a cleaner and simplified one-piece roller design, we have been able to make the on-wing installation easier for the aircraft mechanic by reducing the number of components.”
Rivera suggests there are opportunities for several Canadian King Air operators to be early adopters of the flap roller kits. Operators in Manitoba and Saskatchewan, in particular, are showing interest in a field trial collaboration as they operate scheduled daily flights.
For U.S. registered King Air 200/300 Series, pending an FAA STC, the Field Approval (FAA Form 337) process may be used to secure aircraft serial number specific approval for installation of the Marsh Brothers Aviation Grease-Free flap rollers.
[ENDS]
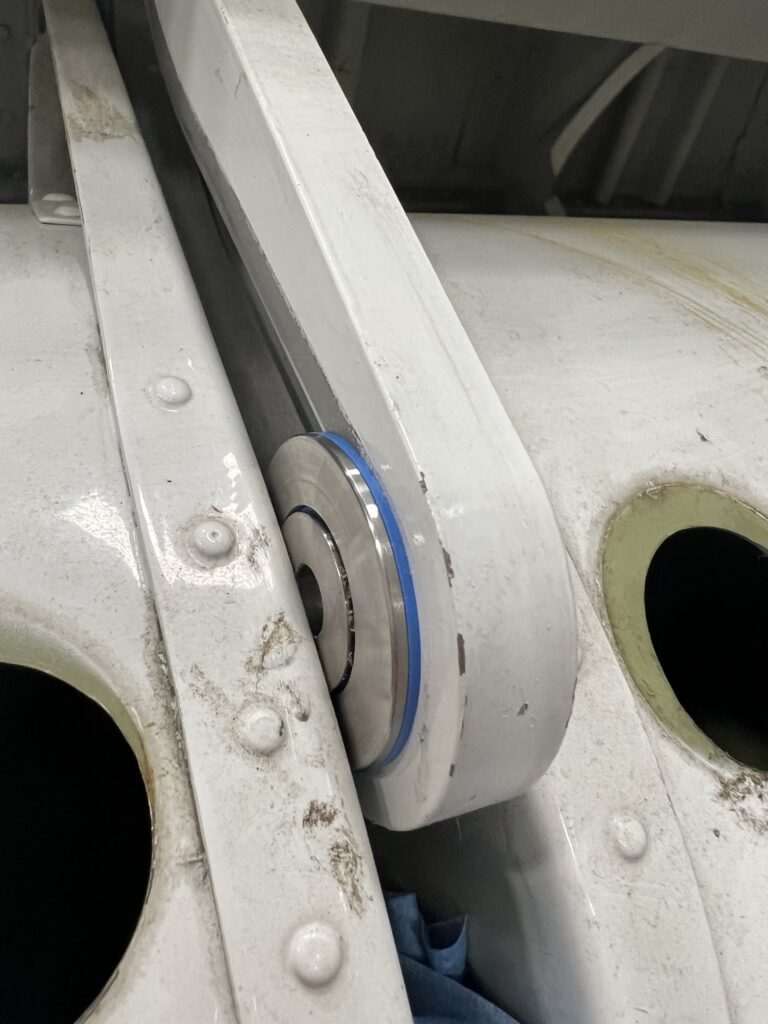
About Marsh Brothers Aviation
Marsh Brothers, a Thomson-Gordon Group company, designs, engineers and manufactures proprietary self-lubricating and grease-free polymer technologies to improve the performance, reliability and service costs for aircraft owners, manufacturers and maintainers. Marsh Brothers’ polymers replace traditional metal bearings, seals and washers reducing component weight by over 80% in comparison. Less weight equals more fuel savings. Typical application includes landing gear pneumatic struts (bearings, dynamic seals and piston wipers), landing gear structures (link bushings), hydraulic actuators (seals, glands, piston rod wipers), flight controls (hinge bushings, rollers), passenger and cargo door hinge bushings and rollers.
Visit: https://www.marshbrothersaviation.com/