Thordon Bearings has reduced the excessive water leakage, that was resulting in costly downtime for the operator of the Limestone Generating Station in Manitoba, Canada, with the company’s SXL shaft seals running for more than three years without the need for replacement.
In an early 2021 proof-of-concept installation, one of the facility’s 133MW turbines had its carbon graphite shaft seal segments upgraded to SXL shaft seal segments. This upgrade reduced leakage by 70%, restoring the system to normal operational levels.
The new Thordon seal segments are expected to last more than 10 years without the need for maintenance or replacement, which is over 5 times the life of the carbon graphite seals it replaced.
The 1300 MW run-of-the-river power station located 750 kilometres (466 miles) north of Winnipeg has 10 propeller type turbines powered by the lower Nelson River. The station was completed in 1992, and the original seals’ faces have required replacement annually to avoid the wear that causes leakage and loss of head pressure – a six-figure financial problem each time a turbine is brought offline for a week.
The three-ring radial seal installed on the 1250mm (49.2in) diameter shaft includes 18 seal segments—half the number used in the previous design. The first stage seal is reversed relative to the two upper rings, allowing higher-pressure injection flow between the first and second rings. This flow acts as a lubricant, coolant, and barrier to prevent abrasives in the turbine water from entering the seal.
A steady supply of abrasive-free water is an important element to ensure long, predictable, bearing and seal wear life, and Thordon’s self-contained water conditioning and monitoring package was part of the supply at Limestone. The system ensures that an adequate supply of clean water is consistently being delivered to the shaft seal.
Greg Auger, Commercial Director at Millstream Engineering, Thordon’s distributor for hydropower customers in Ontario and Western Canada, helped organise the installation. “Prior to our involvement, other companies had looked at the situation and just done more of the same. Without the superior performance offered by SXL the problem would have remained unsolved.”
Business Development Manager – Hydro & Industrial at Thordon Bearings, Ryan Edmonds, said: “Thordon’s SXL has a proven track record as a segmented shaft seal replacing carbon graphite and phenolic seal segments. With our in-house engineering, we have ensured optimised designs that maximise the performance of our proprietary SXL material.”
Maximum interface pressure and minimum leakage rate for Thordon SXL segmented shaft seals are generally similar to those for carbon graphite or phenolic seals. They can operate with the maximum sealed water pressure of over 0.7 MPa (100 psi) and have been installed on shafts up to 3900mm (153.5in) in diameter.
SXL seals can be designed for use in either radial or axial sealing systems. The shaft seal may be located below or above the turbine guide bearing depending on whether a water-lubricated, or oil-lubricated bearing solution is used. Additional advantages of the SXL segmented seal design include easy installation and replacement of all seal components without removing the shaft or disassembly of any major structural components.
“Thordon’s design capabilities and 40+ years of hydro-turbine experience ensure that a fully engineered solution is always provided,” says Edmonds. “Thordon SXL seals offer superior wear resistance, long wear life, and lower maintenance costs for significantly lower life-cycle costs.”
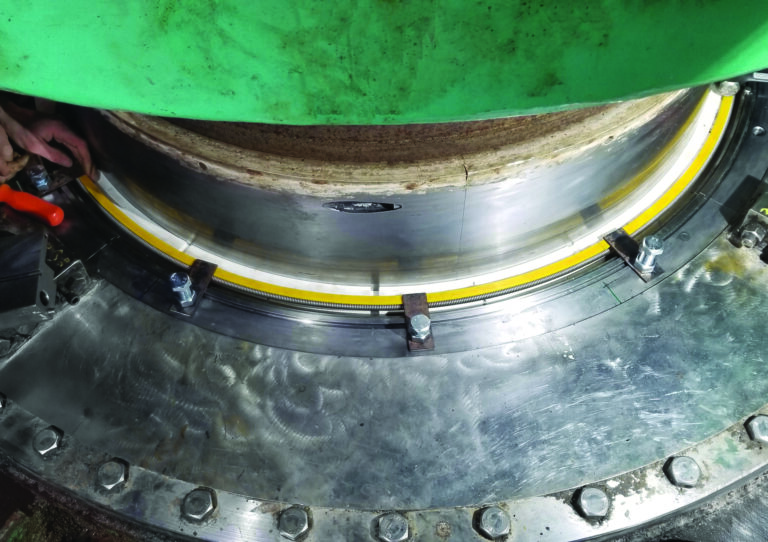
About Thordon Bearings
Thordon Bearings designs and manufactures a complete range of journal bearing and seal systems for application across a number of sectors, including marine, offshore, clean power generation, mining and other pump and land-based industrial sectors. Thordon Bearings’ polymer bearing solutions offer excellent wear life, reduced noise and low operating friction while providing a dependable, long-lasting, environmentally friendly alternative to grease and oil-lubricated bearings. Thordon systems and bearings are available worldwide through over 70 agents and distributors.